What do You Understand by Lean Process Improvement?
Are you in a service industry, mature industry, or in any other organization that handles few trades? Perhaps the Theory of Constraints or Lean thinking can work better for you.last updated Monday, July 8, 2024
#Process Improvement #Lean Process
| by John Burson |
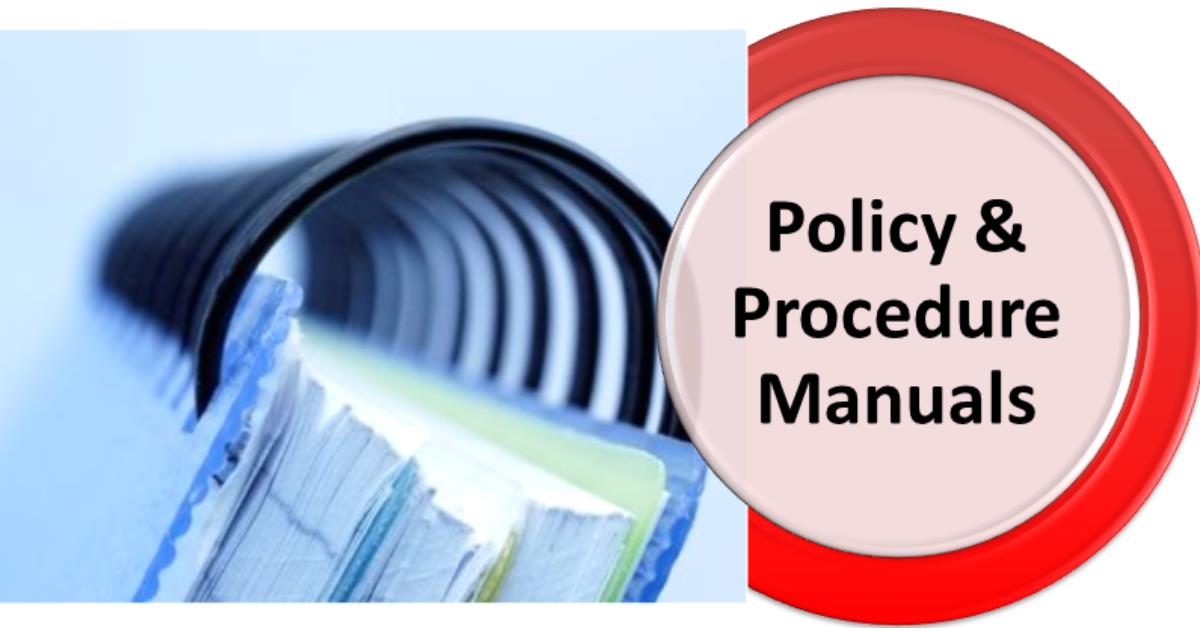
QUICK LINKS
AD
Get access to EB 5 Visa Investment Projects
What is Lean Process Improvement?
Lean Thinking
Have you ever wondered what lean thinking means? As the name implies, it’s a way of viewing the world. Lean is all about removing waste, focusing, and increasing the customer's value. It is also about process flows, engaging in activities that add value to the customer, and eliminating activities that don’t. Adding value also means generating revenue. If something doesn’t generate revenue, it will add costs, not weight.
Lean Process Flow
Follow these basic steps to assess lean operations:
- Determine the structure of activities
- Identify some of the activities that add value
- Allow clients to pull services or products
- Eliminate all activities that don’t add value to your business
- Improve the process
Companies that have very short order-to-delivery cycles are lean operations. This means that they have a strong cash cycle.
Lean 5S System
The lean 5S system of organization is another vital tool used in lean thinking. A messy desk, workplace, or manufacturing cell only makes it difficult to find things, quickly introduces mistakes or accidents, and it’s straightforward to get distracted. The 5S stands for:
- Sort,
- Set in Order,
- Shine,
- Standardize,
- Sustain.
The skeletal system is more visual, Zen-like, and even picturesque. This is because it’s a state of mind and doesn’t require any mathematical analysis like in Six Sigma.
Lean Thinking vs. Six Sigma
The Six Sigma process views process variation as waste. On the other hand, lean thinking focuses more on process flow and regards other activities that don’t add value to destruction. The Six Sigma approach uses statistics to determine any variations. In contrast, lean uses visuals such as flowcharting, process mapping, visual dashboards, and value stream mapping to understand the process flow.
Lean thinking is more suitable for mature, slow-growth, low-transaction industries or organizations that don’t often use mathematical tools. It also focuses on cutting costs. You must balance the resources released for lean or Six Sigma improvement programs.
Lean Process Improvement
Lean thinking can work best when running a slow-growth, mature, non-math, or low-transaction business.
Free Consultation
Similar Pages
- 5 Essentials for a successful Business Process Mapping
- 5 Major Business Problems that Business Process Automation Solves
- Policies and Procedures to Include in Your Employee Handbook
- Guidelines For Writing Policies and Procedures
- What you Should Include in Your Restaurant Employee Policies
- Importance of a Policies & Procedures Manual in Succession Planning
- Standard Operating Procedure Manual: Human Resources
- Policies and Procedures for a Concession Stand
Popular
Benefits of the EB-5 Visa Program | Guide
Search within Paperfree.com